
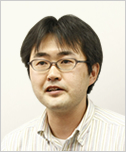
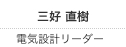
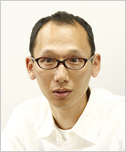
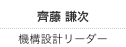

小型化、軽量化は、すでにtypeTやtypeGという先例がある。しかし、高性能なデバイスを詰めこんだtype Zでは同じアプローチのみでは実現できなかった。旧type Sから約10%のフットプリントを縮小するためには、基板や排気機構で約40%もの縮小が必要とされたのだ。
開発の初期段階で13.1インチ液晶ディスプレイの採用が決定したときtype Z全体のサイズも決まった。フットプリントは旧type Sに比べて約10%縮小されることになった。だが、開発にとってはそう簡単な話ではない。CPUやメモリー、各種チップ、光学ドライブなど、大きさの決まっているデバイスは多い。それらを小さくすることはできないので、そのしわ寄せは基板部分と排気機構に集中した。
電気設計リーダーの三好 直樹は、開発の苦労を次のように語る
フットプリントの縮小は、type Zの小型化、軽量化のために必須条件でした。しかし、それを実現するには、マザーボードの基板を旧type Sに比べて約40%も縮小しなくてはいけなかったのです。しかもCPUやグラフィックも高速化しているので、基板には高速な信号に耐えうる構造が必要でした。
強度、信頼性を高めるために、配線は基板の表面にはなるべく出さずに、レイヤーの中に収め、表面にはチップを置くことにしました。その結果、基板は12階層になりました。
1枚の板に見えるtype Zのマザーボードの基板内部は、12層になっており、そこに膨大な配線が引かれ、各デバイスを結んでいる。開発では、CADという設計専用のソフトウェアを用いるのだが、その構造があまりにも複雑になったために、最終的にはCADソフトウェアの自動機能では対応不可能になり、人の手により配線を一本ずつ微調整していったほどだ。
type Zの小型化を実現するには、CADソフトウェアで設計した後に、5ミクロンというような単位で微調整が必要でした。これまで手がけてきたtype Tやtype Gでの経験が生きていたと思います。そういう微調整をすべての基板でやったからこそ、マザーボード40%縮小が実現できたのです。
このような微妙な設計がスムーズに製造までつながったのは、企画、設計、製造の担当者がひとつのところに集まっている長野テックだったからと三好は続けた。
企画、設計、製造が初期状態から会議の場を持ち、意見をぶつけ合い、実現可能なこと、不可能なこと、将来的に考え得る問題点などを一つ一つ吟味しました。これだけ緻密な設計になると、製造段階に入ってから問題が出たとしても容易に修正ができなくなるのです。最初から設計し直しになるといってもいい。それを避けるには、企画の段階で製造まで見通した目が必要でした。企画、設計、製造が一カ所に集約している長野テックだからこそ実現できたことだと思います。
ビジネス用途で使われるノートPCの故障原因は、落下がもっとも多い。そこでtype Zでは落下に強い構造にすることに注力した。例えばビス(基板を筐体に固定するネジを入れる穴)の位置だ。
機構設計リーダーの齊藤 謙次は、開発経緯を次のように語った。
ビスの位置は設計に入る前に決めました。ビスの位置を変えた基板をいくつも用意して落下テストを繰り返し、もっとも強度を維持できるビスの位置を決めてから、設計に入りました。設計後にビス位置を変えるのは至難の業。ほかにも設計前にハードディスクの位置なども落下テストを繰り返し、最適な空間を検討しています。このような手法も長野テックだったからできたことと言えるでしょう。
小型化、軽量化を実現しても壊れやすければダメ。堅牢性を確保してこそ、小型化、軽量化の意味があるわけですから。落下に強いノートPCは、お客様にとっての安心につながります。
※本製品の品質試験は無破損・無故障を保証するものではありません。

